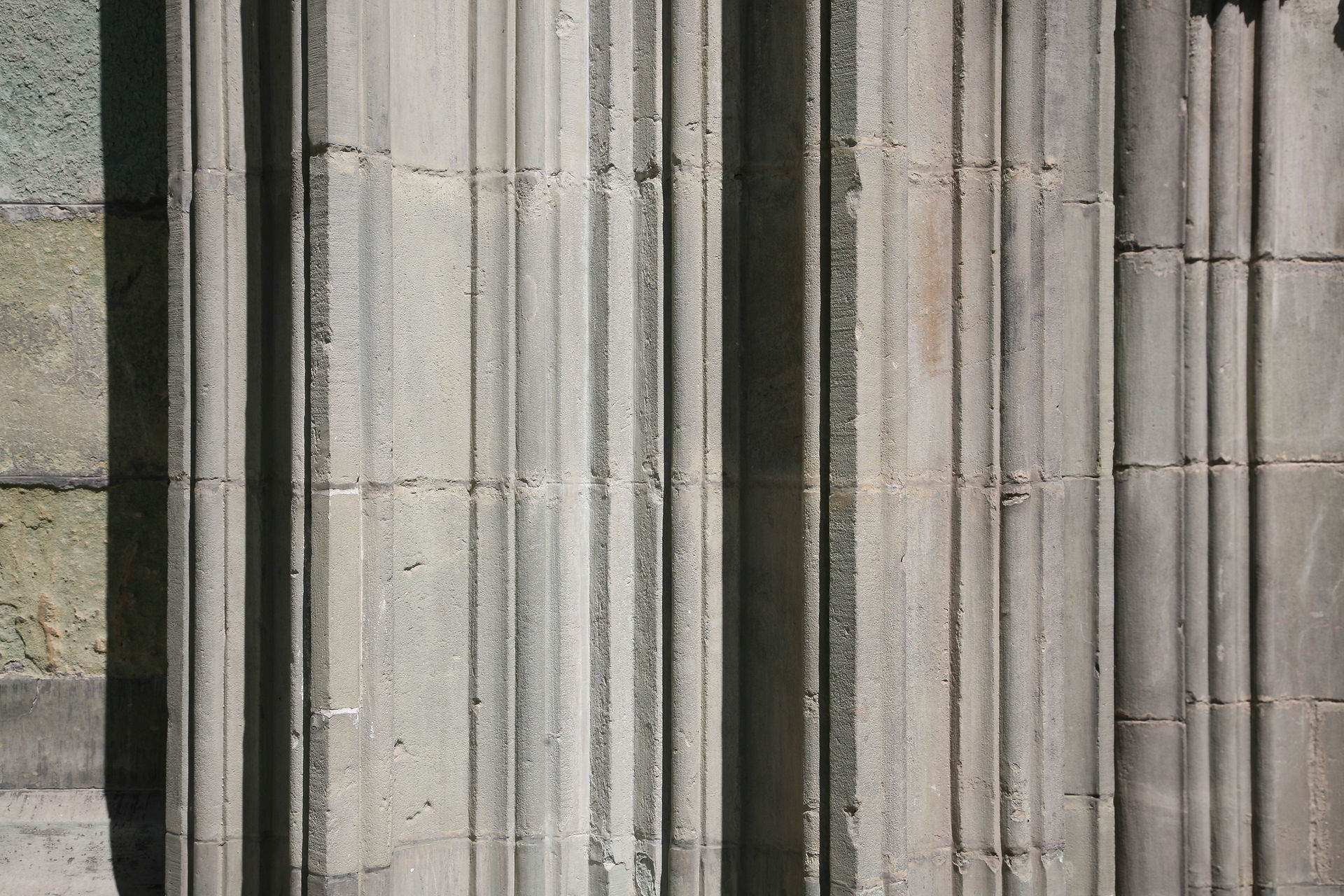
Workshop:
Lean Analytics - Problem Solving, Improvement, Innovation
Workshop Description
Lean organizations are characterized by learning cultures that mobilize the experience and intelligence of their members in the continuous improvement and innovation of all operations and processes. A set of integrated methodologies grounded in the Shewhart Circle/PDCA philosophy enables everyone from the shop floor to the office to apply analytical tools to control existing problems and design effective countermeasures. Standardization, continuous improvement and innovation prepare the organization for future challenges and opportunities, creating additional customer value through systematic development of the workforce.
This workshop introduces operational and support leaders to a structured analytical system that combines a variety of approaches proven to be effective in the control of problems and design of future operational states. It involves participants through a mixture of presentations, discussions and hands-on assignments, focused on critical challenges they have identified in their own work environments. The workshop timeframe can be expanded to allow hands-on application of learned skills to the specific work environment of its participants.
​
Curriculum
The Lean Learning Family: The lean learning family comprises standardization, problem-solving to return performance to compliance with standards, continuous improvement to raise standards, and discontinuous improvement or innovation, guided by a policy deployment (hoshin kanri) framework. Grounded in adult learning principles, various approaches and tools are examined in their effectiveness in different contexts.
Mistakes, Errors and Failures:A systematic distinction between mistakes, errors and failures allows participants to locate different types of sources of problems, including so-called wicked problems, and develop appropriate countermeasures at the levels of knowledge, behavior and systems, including product and process design.
​
Analytical Tools: Participants learn about and then practice a range of analytical tools useful in problem-solving and continuous improvement. A discussion of observation and data collection methods prepares them for the hands-on experience in constructing cause-and-effect diagrams, five-why tree diagrams and various other approaches borrowed from the quality movement. Environmental and sustainability concerns are also addressed.
Decision Tools: After identifying root causes and contributing factors to existing problems or defining improvement objectives, decisions must be made on how to bring change to the organization. This module addresses formal and informal brainstorming, affinity sorts, multi-voting, the use of decision-matrices, and a very powerful methodology to make complex decisions, Choosing by Advantages (CBA). Considerations for the implementation of countermeasures and innovations, confirmation of their effectiveness and approaches to overcoming resistance to change in the implementation environment are also part of this module.
Building a Culture of Continuous Improvement: Problem solutions and improvements are only sustainable if they become part of the culture of the organization. This is the most difficult aspect of successful change. This module showcases the most current research conducted at Toyota and other world-class organizations on effective practices to focus the discretionary contributions of all members of the organization on its improvement, including suggestion systems that work, quality circles and the necessary support structure at the levels of management behavior and policy.
​
Target Audience (Experience):
Suitable for anyone on the lean journey, especially for those with operational or managerial responsibilities and those new to lean support roles.
Target Audience (Organizational Role):
Leaders at all levels.
​
Duration: Three to five days, including genba activities - available on site.